Unlock with AI
Discover how Captivix helped a leading manufacturer streamline their Bill of Materials, reduce costs, and improve efficiency using cutting-edge AI technology. Read the full case study to learn more.
Navigating Complexities of BOM in Manufacturing
A leading industrial equipment manufacturer, known for delivering custom-built machinery, faced a recurring challenge: generating complex Bills of Materials (BOMs) for each order. With high variability and customization, the engineering team spent weeks manually creating accurate BOMs for every project.
- Each order required 6–7 engineers and 2–4 weeks to finalize the BOM.
- Engineers had to assess part availability, vendor lead times, and cost feasibility—all manually.
- The process was labor-intensive, error-prone, and significantly impacted delivery timelines.

Steps to Success
Captivix initiated the engagement with an AI Innovation Workshop, bringing together key stakeholders to identify pain points and opportunities. The BOM creation process stood out as a high-impact, automation-ready use case.
Step 1: AI Innovation Workshop
Captivix kicked off the engagement with a cross-functional AI Innovation Workshop involving engineering, IT, and operations teams. The goal was to align business challenges with AI opportunities.
- Mapped the full lifecycle of BOM creation
- Identified inefficiencies, manual dependencies, and data gaps
- Evaluated AI readiness (data quality, systems, workflows)
- Prioritized BOM optimization as the most impactful and feasible use case
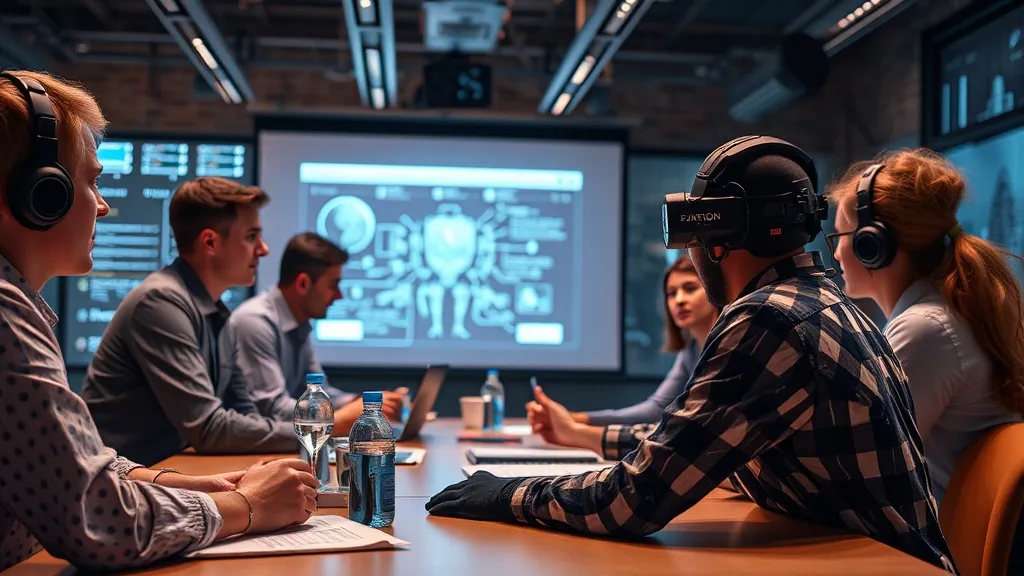
Step 2: Data & Process Analysis
Our team conducted a deep dive into existing engineering workflows and data ecosystems:
- Collected historical BOMs, vendor catalogs, and procurement data
- Reviewed ERP integrations and engineering design tools
- Identified variables influencing BOM decisions like lead times, part specs, and costs
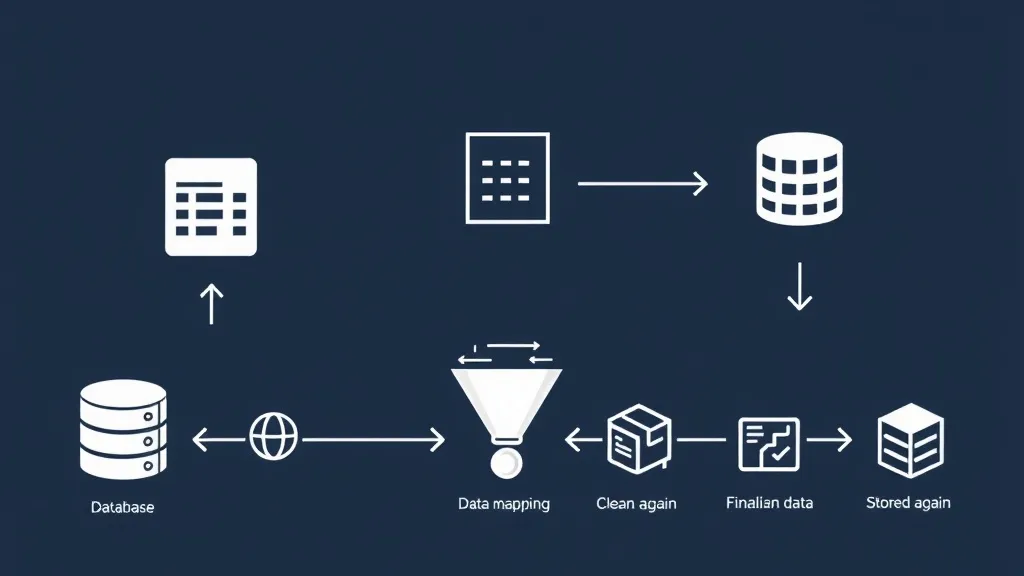
Step 3: AI Model Design & Development
We selected a hybrid AI model architecture based on the complexity of the BOM structures
- Used Transformer-based NLP models (GPT, BERT) for text and spec parsing
- Applied Graph Neural Networks (GNNs) to understand part dependencies
- Introduced Reinforcement Learning (RL) for adaptive optimization of parts selection
- Leveraged AutoML frameworks to accelerate model tuning and performance testing
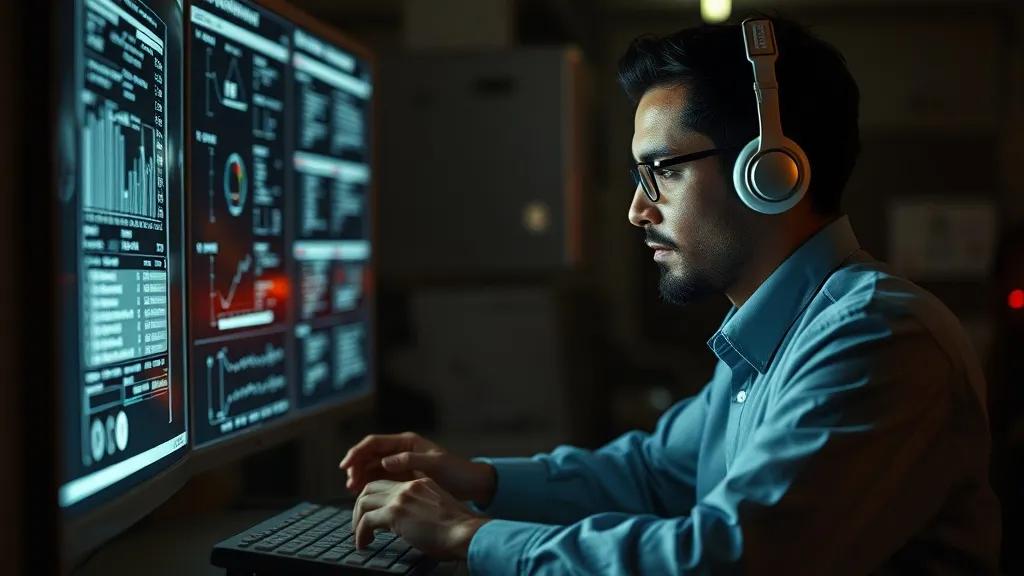
Step 4: Proof of Concept (PoC) Execution
A prototype AI system was developed and integrated into the existing BOM toolchain. The AI-generated BOMs were reviewed by a senior engineer for validation, enabling a human-in-the-loop workflow that balanced automation with quality assurance.
- Generated BOM drafts based on customer requirements and historical patterns
- Pulled live data from vendor systems to optimize selections.
- Conducted multiple test cycles to validate speed, accuracy, and usability
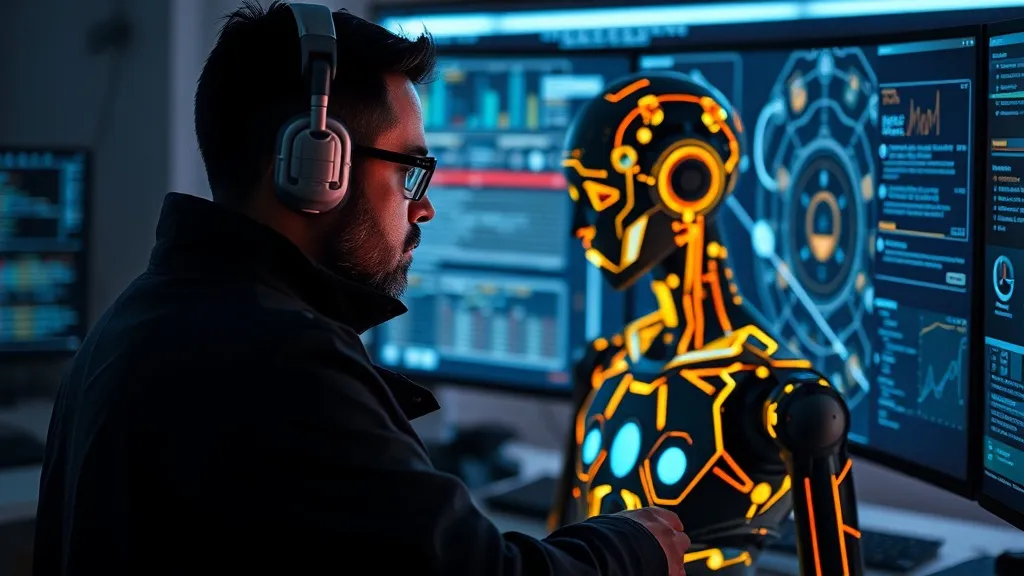
Step 5: Integration & Scalability Planning
Following PoC success, Captivix designed a plan to scale the solution. This is work in progress.
- Integration with broader ERP systems
- Expansion to multiple product lines
- Continuous learning loop to improve the AI engine with each order processed
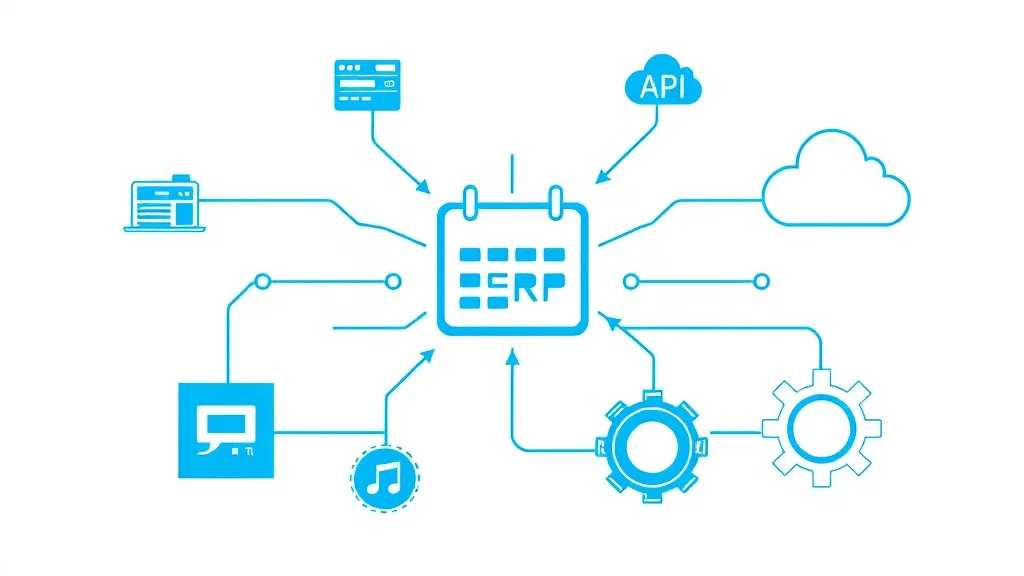
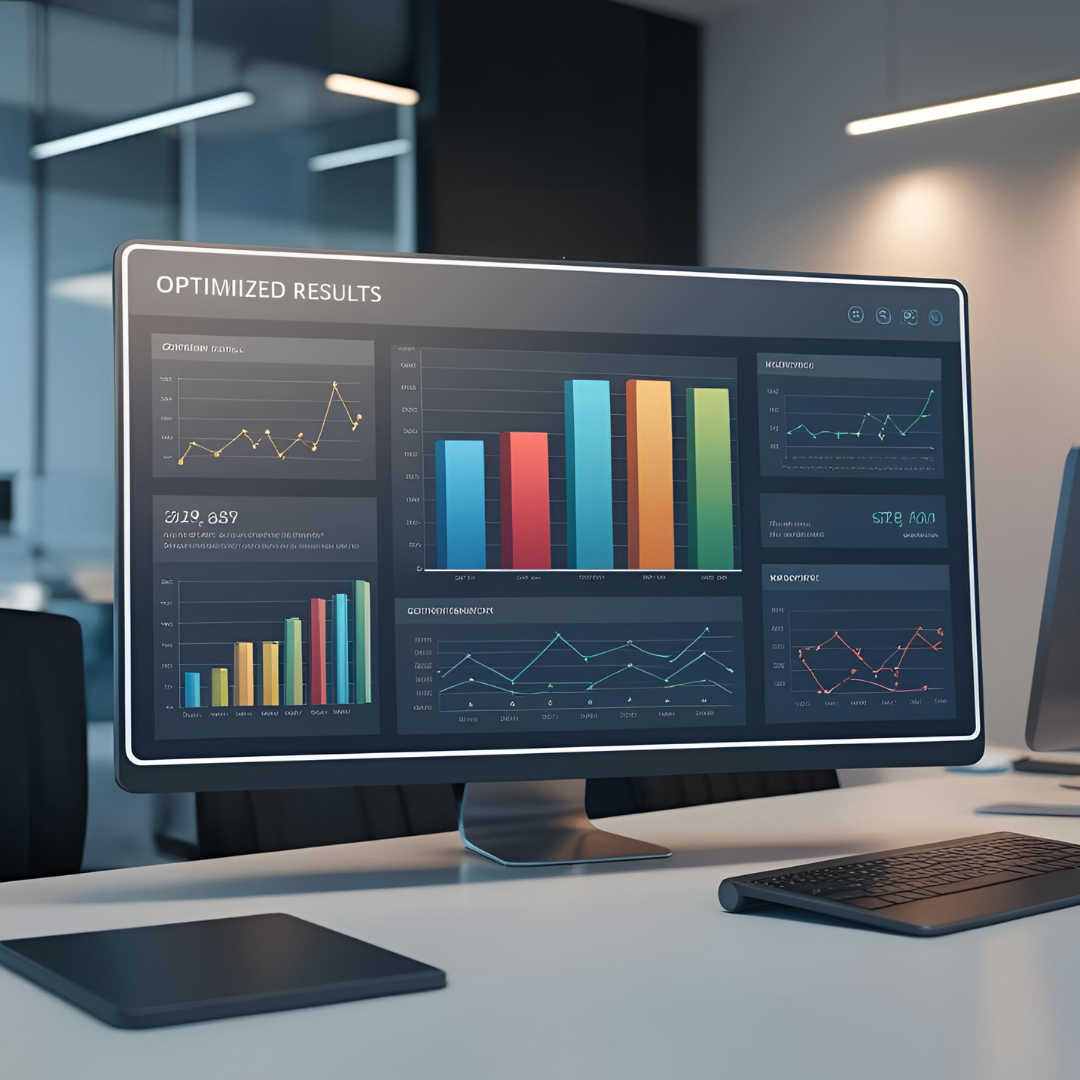
Significant Cost Reduction and Efficiency Gains
Our AI-driven BOM optimization solution delivered substantial results for the client. We achieved a 30% reduction in material costs, a 35% improvement in production efficiency, and a 15% decrease in time-to-market for new products. These improvements directly contributed to increased profitability and a stronger competitive position.
- 95% reduction in planning time
- Improved accuracy and cost control
- 15% decrease in time-to-market